La composizione chimica della sabbia ceramica è principalmente Al2O3 e SiO2, e la fase minerale della sabbia ceramica è principalmente fase corindone e fase mullite, oltre a una piccola quantità di fase amorfa.La refrattarietà della sabbia ceramica è generalmente superiore a 1800°C, ed è un materiale refrattario alluminio-silicio ad alta durezza.
Caratteristiche della sabbia ceramica
● Elevata refrattarietà;
● Piccolo coefficiente di dilatazione termica;
● Elevata conducibilità termica;
● forma sferica approssimativa, piccolo fattore angolare, buona fluidità e capacità compatta;
● Superficie liscia, senza crepe, senza urti;
● materiale neutro, adatto a vari materiali metallici di colata;
● Le particelle hanno un'elevata resistenza e non si rompono facilmente;
● La gamma di dimensioni delle particelle è ampia e la miscelazione può essere personalizzata in base ai requisiti del processo.
Applicazione di sabbia ceramica nelle fusioni di motori
1. Utilizzare sabbia ceramica per risolvere le venature, l'adesione della sabbia, il nucleo rotto e la deformazione del nucleo di sabbia della testata in ghisa
● Il blocco cilindri e la testata sono i pezzi fusi più importanti del motore
● La forma della cavità interna è complessa ei requisiti di precisione dimensionale e pulizia della cavità interna sono elevati
● Grande lotto

Al fine di garantire l'efficienza produttiva e la qualità del prodotto,
● Generalmente si utilizza la linea di assemblaggio per la produzione di sabbia verde (principalmente linea di styling idrostatica).
● Le anime in sabbia generalmente utilizzano il processo cold box e la sabbia rivestita di resina (shell core), mentre alcune anime in sabbia utilizzano il processo hot box.
● A causa della forma complessa dell'anima in sabbia del monoblocco e della colata della testata, alcune anime in sabbia hanno una piccola area della sezione trasversale, la parte più sottile di alcuni monoblocchi e anime della camicia d'acqua della testata è di soli 3-3,5 mm e l'uscita della sabbia è stretta, l'anima di sabbia dopo la fusione è circondata a lungo da ferro fuso ad alta temperatura, è difficile pulire la sabbia ed è necessaria un'attrezzatura speciale per la pulizia, ecc. In passato, tutta la sabbia silicea veniva utilizzata nella fusione produzione, che ha causato vene e problemi di adesione della sabbia nelle fusioni della camicia d'acqua del blocco cilindri e della testata.La deformazione del nucleo e i problemi di rottura del nucleo sono molto comuni e difficili da risolvere.
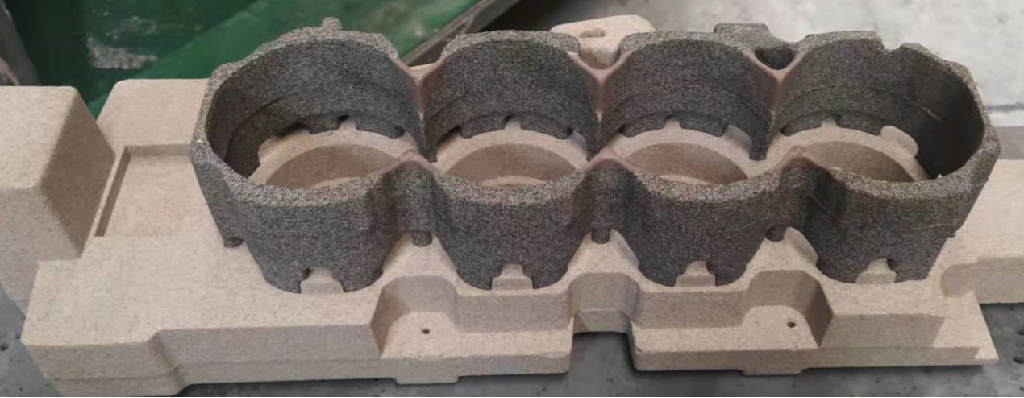
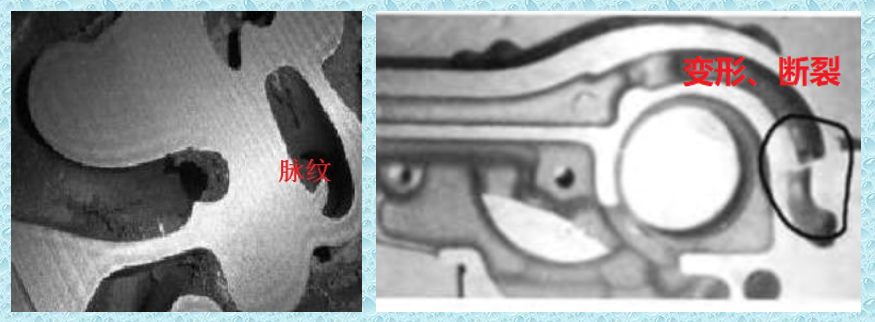
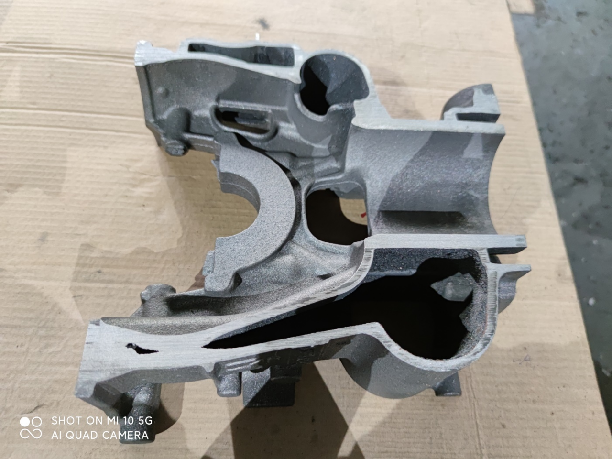
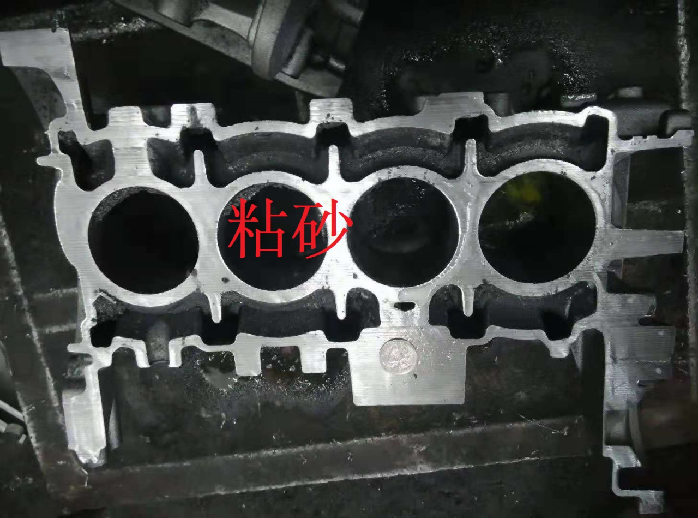
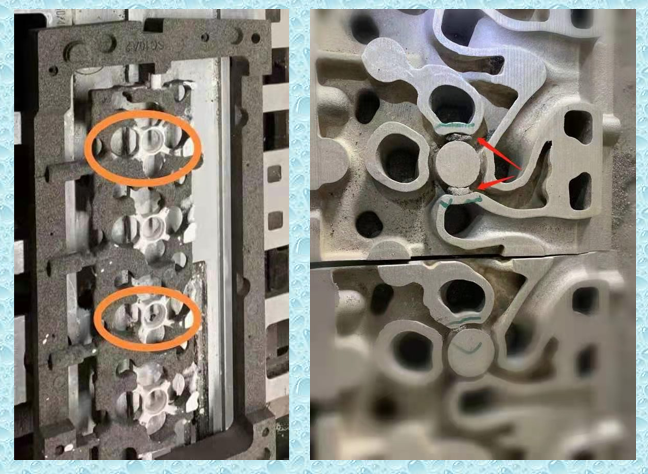
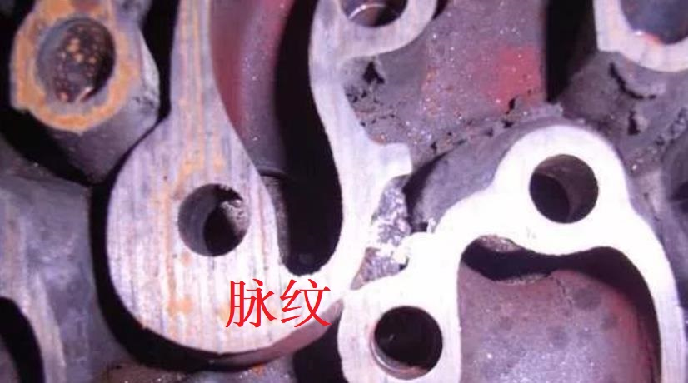
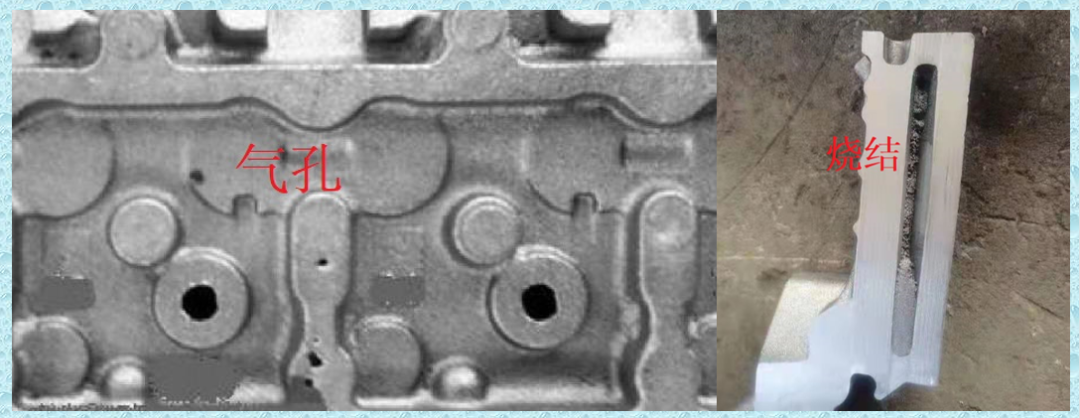
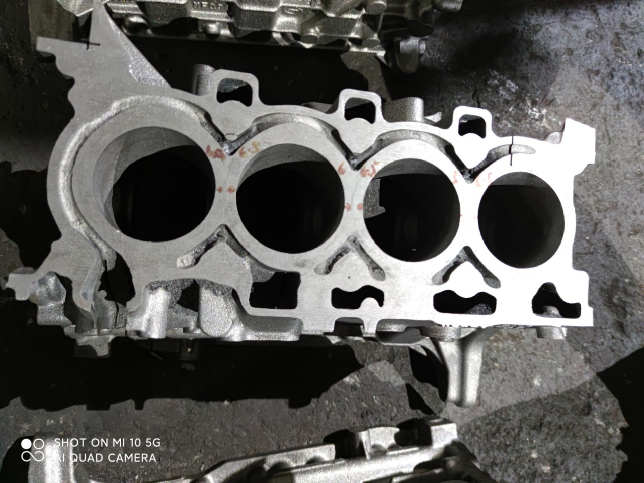
Per risolvere tali problemi, a partire dal 2010 circa, alcune note società di fusione di motori nazionali, come FAW, Weichai, Shangchai, Shanxi Xinke, ecc., hanno iniziato a ricercare e testare l'applicazione della sabbia ceramica per produrre blocchi cilindri, camicie dell'acqua della testata del cilindro e passaggi dell'olio.I nuclei di sabbia uguali eliminano o riducono efficacemente i difetti come la sinterizzazione della cavità interna, l'adesione della sabbia, la deformazione del nucleo di sabbia e i nuclei rotti.
Le immagini seguenti sono realizzate con sabbia ceramica con processo a scatola fredda.
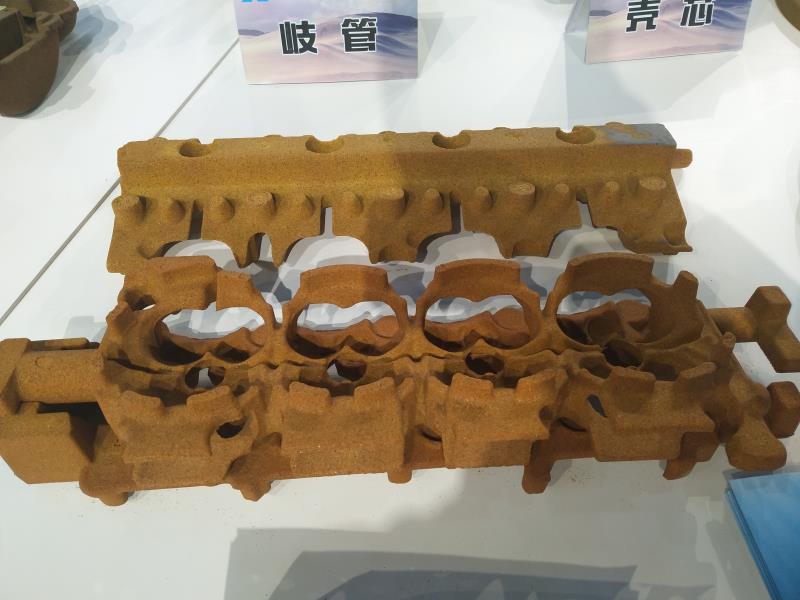
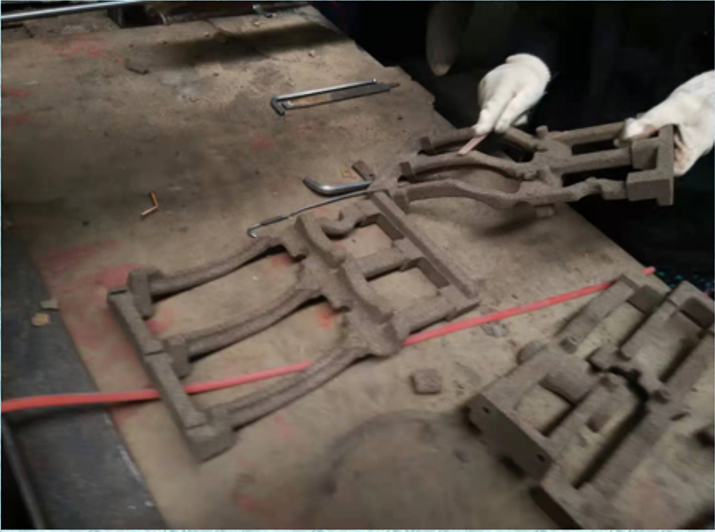
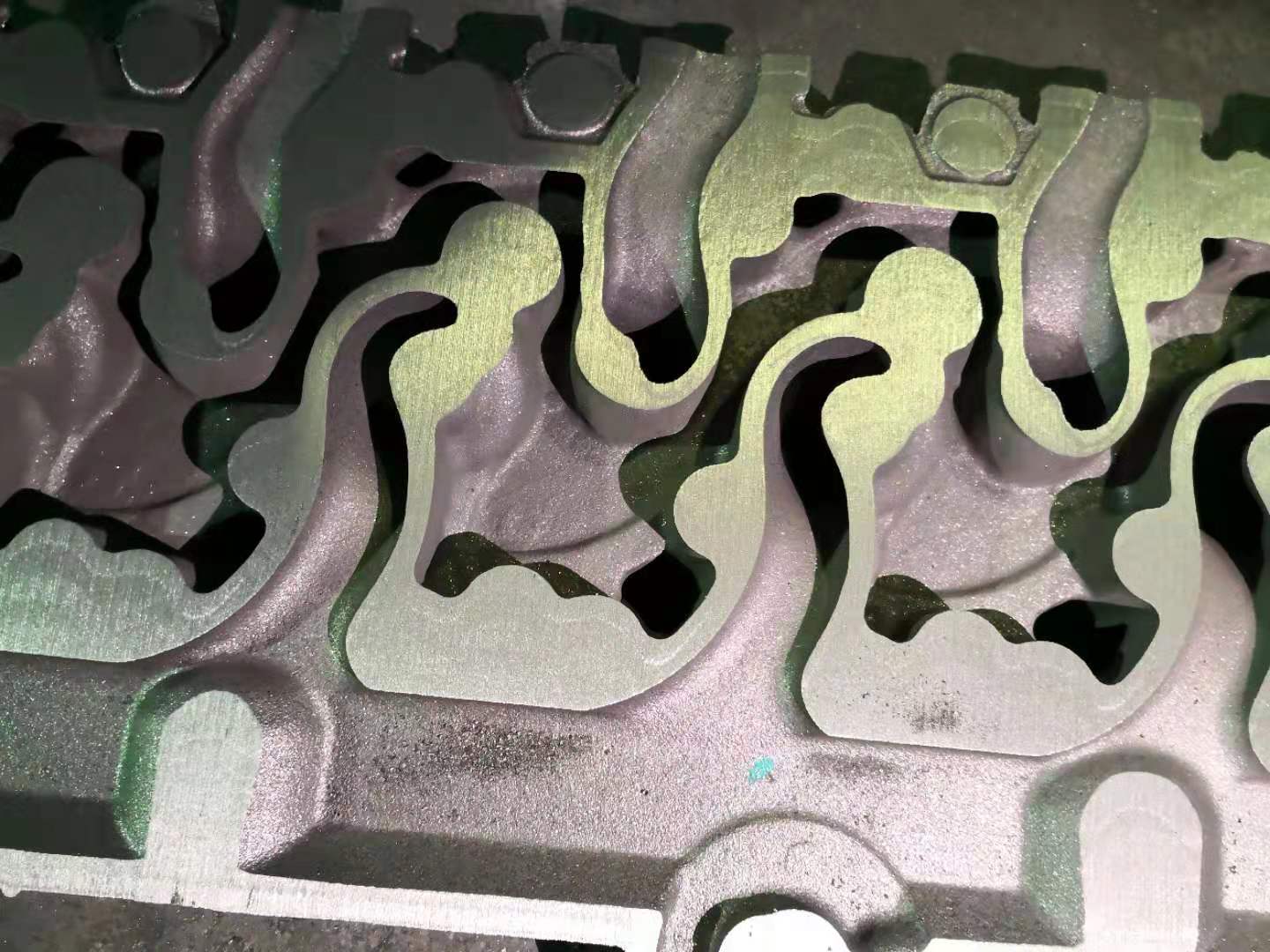
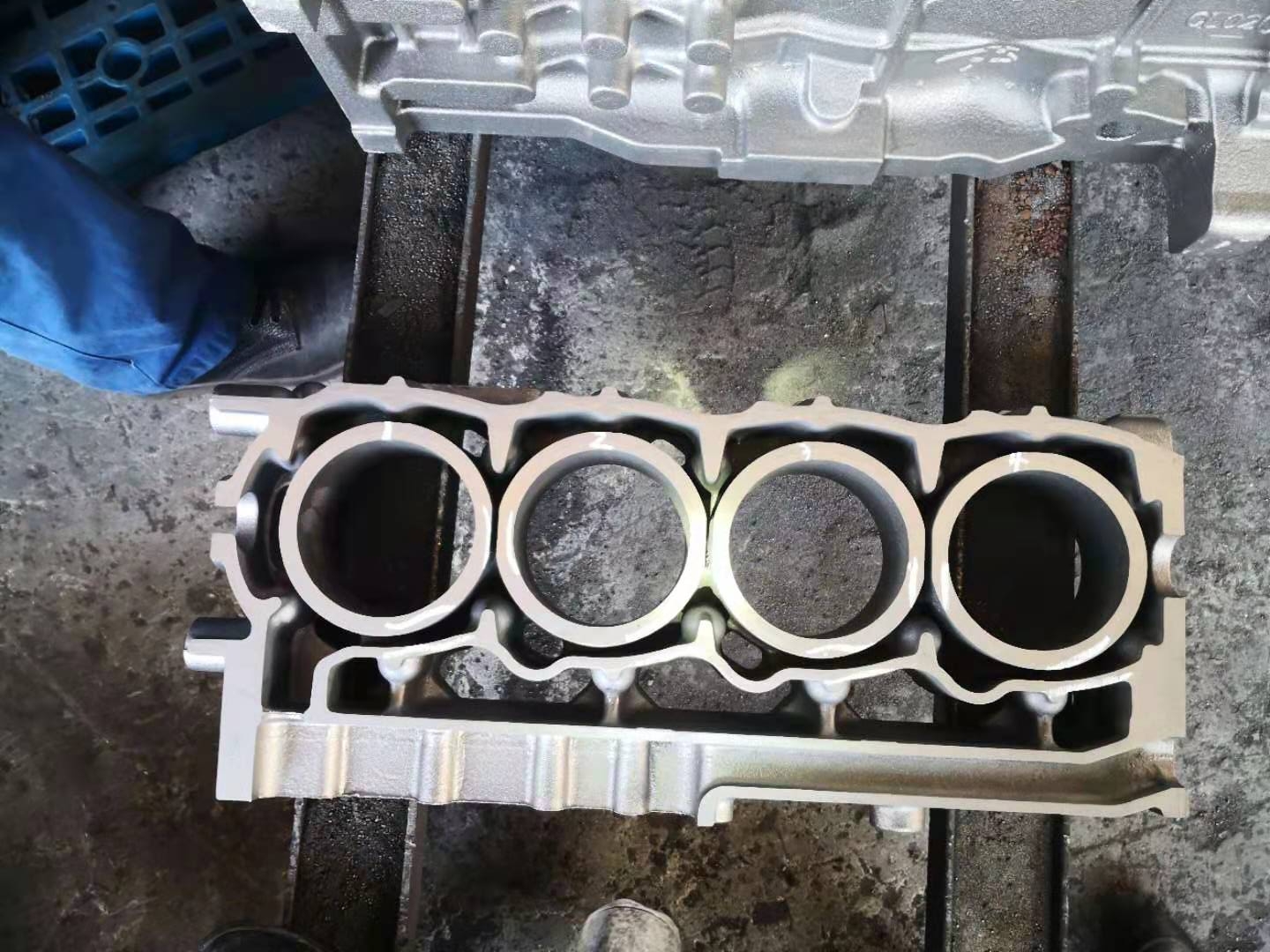
Da allora, la sabbia di lavaggio mista a sabbia ceramica è stata gradualmente promossa nei processi cold box e hot box e applicata ai nuclei delle camicie d'acqua della testata.È in produzione stabile da più di 6 anni.L'uso corrente dell'anima di sabbia della scatola fredda è: in base alla forma e alle dimensioni dell'anima di sabbia, la quantità di sabbia ceramica aggiunta è del 30% -50%, la quantità totale di resina aggiunta è dell'1,2% -1,8% e il la resistenza alla trazione è 2,2-2,7 MPa.(Dati dei test sui campioni di laboratorio)
Riepilogo
Le parti in ghisa del blocco cilindri e della testata contengono molte strutture di cavità interne strette e la temperatura di colata è generalmente compresa tra 1440 e 1500 °C.La parte a parete sottile del nucleo di sabbia viene facilmente sinterizzata sotto l'azione di ferro fuso ad alta temperatura, come il ferro fuso che si infiltra nel nucleo di sabbia, o produce una reazione di interfaccia per formare sabbia appiccicosa.La refrattarietà della sabbia ceramica è maggiore di 1800°C, nel frattempo, la vera densità della sabbia ceramica è relativamente alta, l'energia cinetica delle particelle di sabbia con lo stesso diametro e velocità è 1,28 volte quella delle particelle di sabbia silicea quando si spara sabbia, che può aumentare la densità delle anime di sabbia.
Questi vantaggi sono i motivi per cui l'uso della sabbia ceramica può risolvere il problema dell'adesione della sabbia nella cavità interna delle fusioni della testata.
La camicia d'acqua, le parti di aspirazione e scarico del blocco cilindri e la testata presentano spesso difetti di venatura.Un gran numero di ricerche e pratiche di fusione hanno dimostrato che la causa principale dei difetti delle venature sulla superficie del getto è l'espansione del cambiamento di fase della sabbia silicea, che provoca stress termico che porta a crepe sulla superficie del nucleo di sabbia, che provoca la fusione del ferro a penetrare nelle fessure la tendenza delle venature è maggiore soprattutto nella lavorazione cold box.Infatti, il tasso di espansione termica della sabbia silicea arriva fino all'1,5%, mentre il tasso di espansione termica della sabbia ceramica è solo dello 0,13% (riscaldata a 1000°C per 10 minuti).La possibilità di fessurazione è molto ridotta sulla superficie dell'anima di sabbia a causa della sollecitazione di espansione termica.L'utilizzo di sabbia ceramica nell'anima di sabbia del monoblocco e della testata è attualmente una soluzione semplice ed efficace al problema delle venature.
Le anime in sabbia della camicia d'acqua della testata del cilindro complicate, a parete sottile, lunghe e strette e le anime in sabbia del canale dell'olio del cilindro richiedono un'elevata resistenza (compresa la resistenza alle alte temperature) e tenacità, e allo stesso tempo devono controllare la generazione di gas della sabbia del nucleo.Tradizionalmente, viene utilizzato principalmente il processo di sabbia rivestita.L'uso di sabbia ceramica riduce la quantità di resina e ottiene l'effetto di elevata resistenza e bassa generazione di gas.A causa del continuo miglioramento delle prestazioni della resina e della sabbia grezza, negli ultimi anni il processo cold box ha sempre più sostituito parte del processo con sabbia rivestita, migliorando notevolmente l'efficienza produttiva e migliorando l'ambiente di produzione.
2. Applicazione di sabbia ceramica per risolvere il problema della deformazione del nucleo di sabbia del tubo di scarico
I collettori di scarico funzionano a lungo in condizioni alternate ad alta temperatura e la resistenza all'ossidazione dei materiali alle alte temperature influisce direttamente sulla durata dei collettori di scarico.Negli ultimi anni, il paese ha continuamente migliorato gli standard di emissione degli scarichi delle automobili e l'applicazione della tecnologia catalitica e della tecnologia di sovralimentazione ha notevolmente aumentato la temperatura di esercizio del collettore di scarico, raggiungendo oltre 750 °C.Con l'ulteriore miglioramento delle prestazioni del motore, aumenterà anche la temperatura di esercizio del collettore di scarico.Allo stato attuale, viene generalmente utilizzato acciaio fuso resistente al calore, come ZG 40Cr22Ni10Si2 (JB/T 13044), ecc., con una temperatura resistente al calore di 950°C-1100°C.
La cavità interna del collettore di scarico deve generalmente essere priva di crepe, giunti freddi, cavità di restringimento, inclusioni di scorie, ecc. che influiscono sulle prestazioni e la rugosità della cavità interna non deve essere superiore a Ra25.Allo stesso tempo, esistono norme rigorose e chiare sulla deviazione dello spessore della parete del tubo.Per molto tempo, il problema dello spessore irregolare della parete e dell'eccessiva deviazione della parete del tubo del collettore di scarico ha afflitto molte fonderie di collettori di scarico.

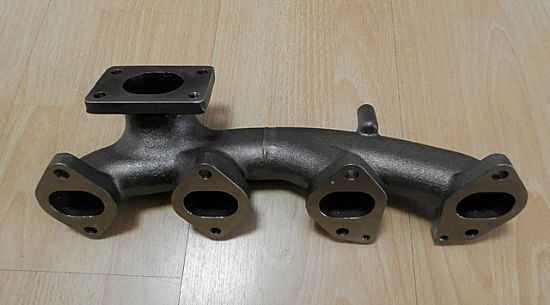
Una fonderia ha utilizzato per la prima volta anime di sabbia rivestite di sabbia silicea per produrre collettori di scarico in acciaio resistente al calore.A causa dell'elevata temperatura di colata (1470-1550°C), le anime di sabbia si deformavano facilmente, con conseguenti fenomeni fuori tolleranza nello spessore delle pareti del tubo.Sebbene la sabbia silicea sia stata trattata con cambiamento di fase ad alta temperatura, a causa dell'influenza di vari fattori, non è ancora in grado di superare la deformazione del nucleo di sabbia ad alta temperatura, con conseguente ampia gamma di fluttuazioni nello spessore della parete del tubo e, nei casi più gravi, verrà demolito.Per migliorare la resistenza dell'anima di sabbia e controllare la generazione di gas dell'anima di sabbia, si è deciso di utilizzare sabbia rivestita di sabbia ceramica.Quando la quantità di resina aggiunta era inferiore del 36% rispetto a quella della sabbia rivestita di sabbia silicea, la sua resistenza alla flessione a temperatura ambiente e la resistenza alla flessione termica sono aumentate del 51%, 67% e la quantità di generazione di gas è ridotta del 20%, che soddisfa il requisiti di processo di elevata resistenza e bassa generazione di gas.
La fabbrica utilizza anime di sabbia rivestite di sabbia silicea e anime di sabbia rivestite di sabbia ceramica per la fusione simultanea, dopo aver pulito le fusioni, conducono ispezioni anatomiche.
Se il nucleo è costituito da sabbia rivestita di sabbia silicea, i getti hanno uno spessore della parete irregolare e una parete sottile e lo spessore della parete è di 3,0-6,2 mm;quando il nucleo è costituito da sabbia rivestita di sabbia ceramica, lo spessore della parete del getto è uniforme e lo spessore della parete è di 4,4-4,6 mm.come segue immagine
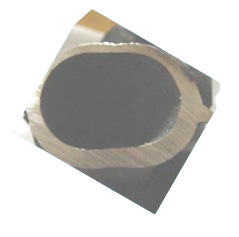
Sabbia rivestita di sabbia silicea
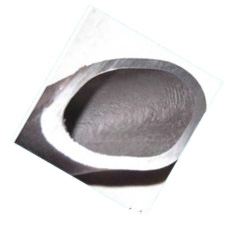
Sabbia rivestita di sabbia ceramica
La sabbia rivestita di sabbia ceramica viene utilizzata per realizzare i nuclei, che elimina la rottura del nucleo di sabbia, riduce la deformazione del nucleo di sabbia, migliora notevolmente la precisione dimensionale del canale di flusso della cavità interna del collettore di scarico e riduce l'adesione della sabbia nella cavità interna, migliorando la qualità di fusioni e prodotti finiti hanno ottenuto notevoli benefici economici.
3. Applicazione di sabbia ceramica nell'alloggiamento del turbocompressore
La temperatura di esercizio all'estremità della turbina del guscio del turbocompressore generalmente supera i 600°C, e alcuni raggiungono anche i 950-1050°C.Il materiale del guscio deve essere resistente alle alte temperature e avere buone prestazioni di fusione.La struttura del guscio è più compatta, lo spessore della parete è sottile e uniforme e la cavità interna è pulita, ecc., è estremamente impegnativa.Allo stato attuale, l'alloggiamento del turbocompressore è generalmente realizzato in fusione di acciaio resistente al calore (come 1.4837 e 1.4849 della norma tedesca DIN EN 10295) e viene utilizzata anche ghisa duttile resistente al calore (come lo standard tedesco GGG SiMo, l'americano ferro nodulare austenitico standard ad alto contenuto di nichel D5S, ecc.).
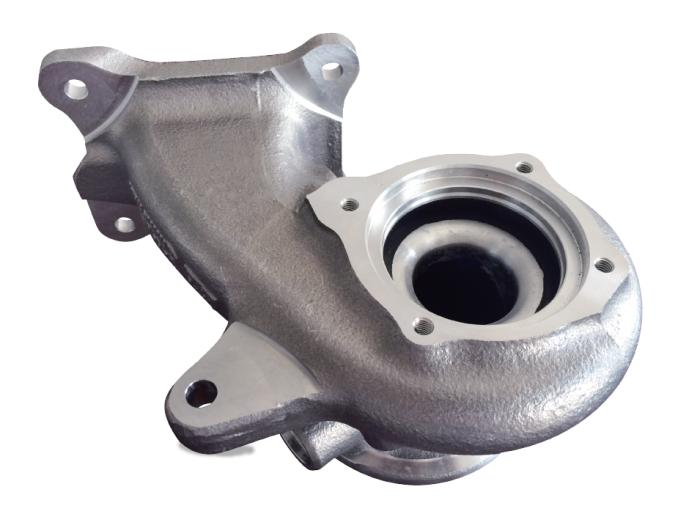
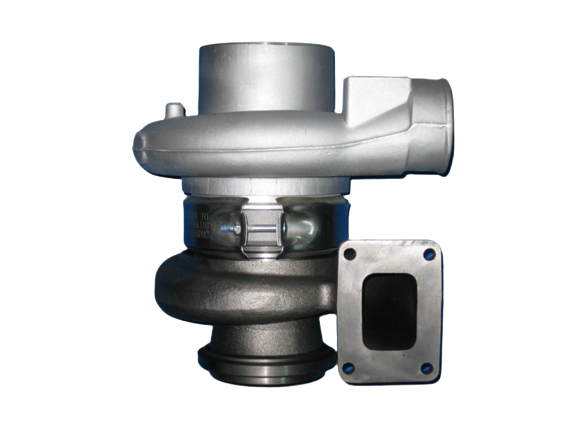
Un alloggiamento del turbocompressore del motore da 1,8 T, materiale: 1.4837, ovvero GX40CrNiSi 25-12, composizione chimica principale (%): C: 0,3-0,5, Si: 1-2,5, Cr: 24-27, Mo: Max 0,5, Ni: 11 -14, temperatura di versamento 1560 ℃.La lega ha un alto punto di fusione, un elevato tasso di ritiro, una forte tendenza alla rottura a caldo e un'elevata difficoltà di colata.La struttura metallografica del getto ha severi requisiti sui carburi residui e le inclusioni non metalliche, e vi sono anche normative specifiche sui difetti di fusione.Al fine di garantire la qualità e l'efficienza produttiva dei getti, il processo di stampaggio adotta la fusione dell'anima con anime in guscio di sabbia rivestite con film (e alcune anime di scatole fredde e scatole calde).Inizialmente, è stata utilizzata la sabbia di lavaggio AFS50, quindi è stata utilizzata la sabbia silicea tostata, ma i problemi come l'adesione della sabbia, le sbavature, le crepe termiche e i pori nella cavità interna sono apparsi a vari livelli.
Sulla base di ricerche e test, la fabbrica ha deciso di utilizzare la sabbia ceramica.Inizialmente acquistata sabbia rivestita finita (sabbia ceramica al 100%), quindi acquistata attrezzatura per la rigenerazione e il rivestimento e ottimizzato continuamente il processo durante il processo di produzione, utilizzare sabbia ceramica e sabbia di lavaggio per mescolare sabbia grezza.Allo stato attuale, la sabbia rivestita è approssimativamente implementata secondo la seguente tabella:
Processo di sabbia ceramica rivestita di sabbia per l'alloggiamento del turbocompressore | ||||
Dimensione della sabbia | Tasso di sabbia ceramica % | Aggiunta di resina % | Resistenza alla flessione MPa | Portata gas ml/g |
AFS50 | 30-50 | 1.6-1.9 | 6,5-8 | ≤12 |
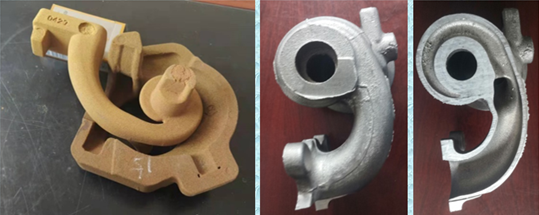
Negli ultimi anni, il processo produttivo di questo impianto ha funzionato stabilmente, la qualità dei getti è buona e i benefici economici e ambientali sono notevoli.Il riassunto è il seguente:
UN.L'utilizzo di sabbia ceramica, o l'utilizzo di una miscela di sabbia ceramica e sabbia silicea per realizzare le anime, elimina i difetti come l'adesione della sabbia, la sinterizzazione, le venature e il cracking termico delle fusioni e realizza una produzione stabile ed efficiente;
B.Fusione dell'anima, alta efficienza produttiva, basso rapporto sabbia-ferro (generalmente non superiore a 2:1), minor consumo di sabbia grezza e costi inferiori;
C.La colata del nucleo favorisce il riciclaggio e la rigenerazione complessivi della sabbia di scarto e il recupero termico viene adottato in modo uniforme per la rigenerazione.Le prestazioni della sabbia rigenerata hanno raggiunto il livello della nuova sabbia per la sabbiatura, che ha ottenuto l'effetto di ridurre il costo di acquisto della sabbia grezza e di ridurre lo scarico dei rifiuti solidi;
D.È necessario controllare frequentemente il contenuto di sabbia ceramica nella sabbia rigenerata per determinare la quantità di nuova sabbia ceramica aggiunta;
e.La sabbia ceramica ha forma rotonda, buona fluidità e grande specificità.Se miscelato con sabbia silicea, è facile causare segregazione.Se necessario, il processo di tiro con la sabbia deve essere regolato;
F.Quando si copre il film, provare a utilizzare resina fenolica di alta qualità e utilizzare con cautela vari additivi.
4. Applicazione di sabbia ceramica nella testata del motore in lega di alluminio
Al fine di migliorare la potenza delle automobili, ridurre il consumo di carburante, ridurre l'inquinamento dei gas di scarico e proteggere l'ambiente, le automobili leggere sono la tendenza di sviluppo dell'industria automobilistica.Allo stato attuale, le fusioni di motori automobilistici (incluso il motore diesel), come blocchi cilindri e testate, sono generalmente fuse con leghe di alluminio e il processo di fusione di blocchi cilindri e testate, quando si utilizzano anime in sabbia, colata per gravità in stampi metallici e bassa pressione casting (LPDC) sono i più rappresentativi.
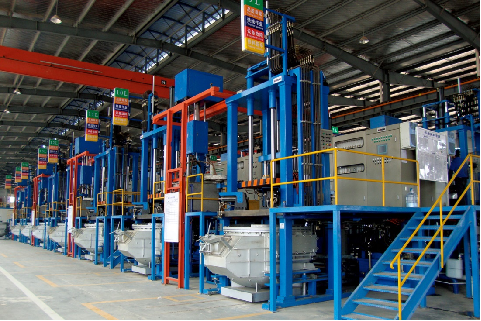
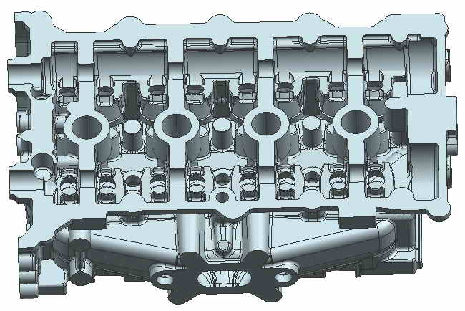
L'anima in sabbia, la sabbia rivestita e il processo cold box del blocco cilindri in lega di alluminio e le fusioni della testata sono più comuni, adatti a caratteristiche di produzione di alta precisione e su larga scala.Il metodo di utilizzo della sabbia ceramica è simile alla produzione della testata in ghisa.A causa della bassa temperatura di colata e del peso specifico ridotto della lega di alluminio, viene generalmente utilizzata sabbia per anima a bassa resistenza, come un'anima di sabbia per scatola fredda in una fabbrica, la quantità di resina aggiunta è dello 0,5-0,6% e la resistenza alla trazione è 0,8-1,2MPa.È richiesta la sabbia del nucleo Ha una buona collassabilità.L'uso di sabbia ceramica riduce la quantità di resina aggiunta e migliora notevolmente il collasso dell'anima di sabbia.
Negli ultimi anni, al fine di migliorare l'ambiente di produzione e migliorare la qualità dei getti, ci sono sempre più ricerche e applicazioni di leganti inorganici (tra cui vetro solubile modificato, leganti fosfatici, ecc.).L'immagine sotto è il sito di fusione di una fabbrica che utilizza la testa del cilindro in lega di alluminio con legante inorganico in sabbia ceramica.
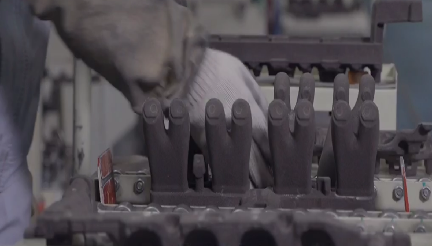
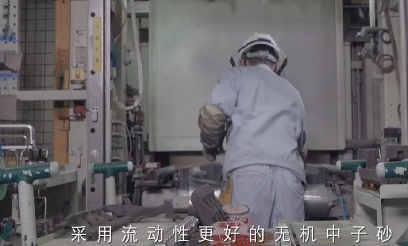
La fabbrica utilizza un legante inorganico di sabbia ceramica per realizzare il nucleo e la quantità di legante aggiunta è dell'1,8 ~ 2,2%.A causa della buona fluidità della sabbia ceramica, il nucleo di sabbia è denso, la superficie è completa e liscia e, allo stesso tempo, la quantità di generazione di gas è ridotta, migliora notevolmente la resa dei getti, migliora la collassabilità della sabbia del nucleo , migliora l'ambiente di produzione e diventa un modello di produzione verde.
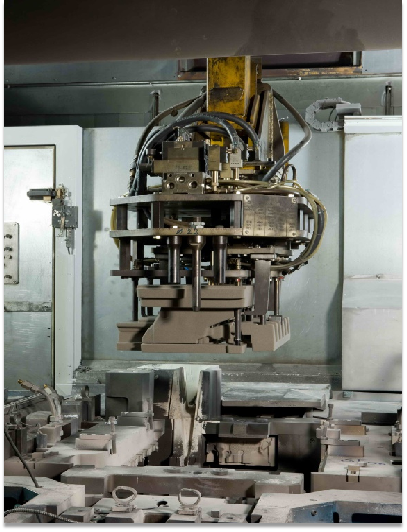
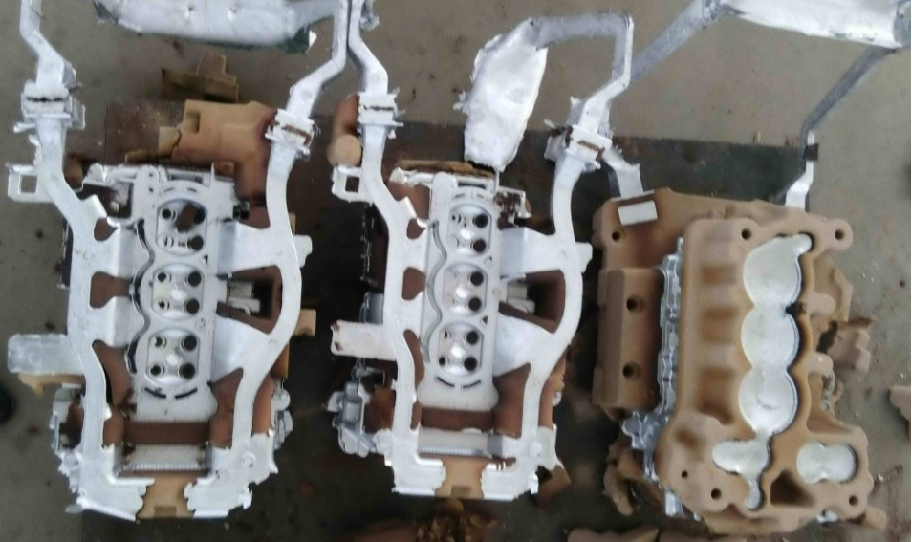
L'applicazione della sabbia ceramica nell'industria della fusione dei motori ha migliorato l'efficienza produttiva, migliorato l'ambiente di lavoro, risolto i difetti di fusione e ottenuto significativi vantaggi economici e buoni benefici ambientali.
L'industria della fonderia di motori dovrebbe continuare ad aumentare la rigenerazione della sabbia del nucleo, migliorare ulteriormente l'efficienza d'uso della sabbia ceramica e ridurre le emissioni di rifiuti solidi.
Dal punto di vista dell'effetto d'uso e dell'ambito di utilizzo, la sabbia ceramica è attualmente la sabbia speciale per colata con le migliori prestazioni globali e il maggior consumo nell'industria della fusione di motori.
Tempo di pubblicazione: 27 marzo 2023